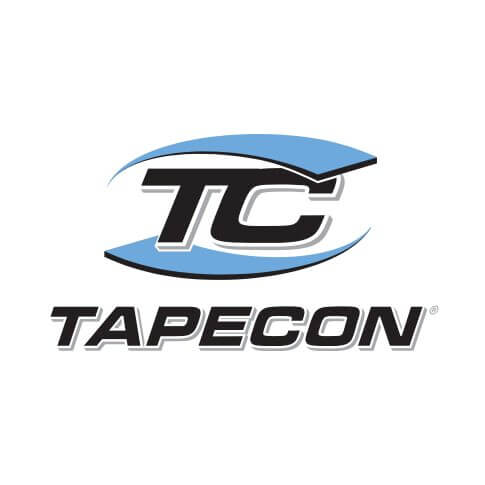
Precision Meets Efficiency: How Tapecon Tackles the Toughest Challenges in Medical Device Manufacturing
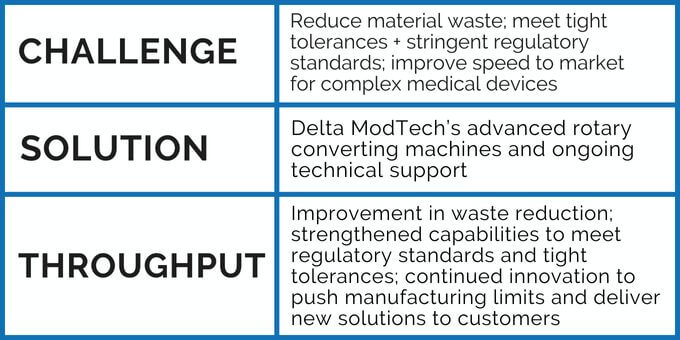
Founded in 1919, Buffalo, NY-based Tapecon is a five-generation family-owned business that has become a leader in medical and industrial manufacturing.
Tapecon’s relentless pursuit of process improvements has a lot to do with its enduring success. But to maintain its edge in the medical device arena in particular, Tapecon must continually find efficient ways to produce highly complex products—products with extremely precise tolerances and stringent standards.
Challenge
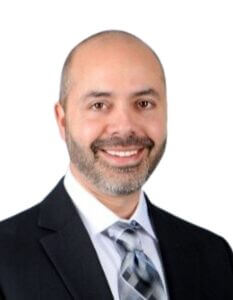
According to Tapecon’s Director of Operations, Michael Gebera, accurately and efficiently manufacturing complex medical devices requires overcoming operational hurdles like these:
Minimizing material waste
Tapecon’s clients expect that the delicate, highly expensive materials involved in the manufacturing of their products will be handled accordingly—with as little waste as possible.
“The need for precise bonding and minimizing material waste initially led us to seek outside expertise.”
Michael Gebera, Director of Operations, Tapecon
Managing strict tolerances
Manufacturing medical devices requires meeting some of the most demanding tolerances in the converting industry.
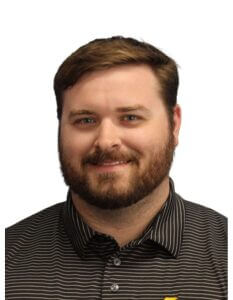
For instance, Ryan Cribbin, Continuous Improvement Lead at Tapecon, highlights the difficulties of working with thick polymers. “When there are strict curl tolerances on a final part, we need to understand how to solve the curl issue that may be present in raw materials.”
Meeting the specs of highly regulated products
Those aforementioned strict tolerances go hand in hand with highly regulated medical device products. Tapecon has to meet those rigorous regulations as well as the standards of its own ISO 13845 and 9001 registered quality management system.
“Not just any machine can help us achieve that level of quality for our customers,” says Gebera.
Integrating complex web processes
Producing medical devices as efficiently as possible often requires combining durable printing and complex converting operations on a single machine.
Cribbin points to the example of laminating two different web materials in register from different manufacturing processes. “It’s important that we can rely on the machine provider’s support to help us get the most from the tools we have—as well as know what add-ons could help us.”
Solution
If challenges like those above can’t be solved, Gebera says the consequences would include “incurring too much waste, driving up costs, and essentially not being a good solutions provider for our clients.”
Fortunately, Tapecon’s exceptional manufacturing capabilities have been complemented—and strengthened—by Delta ModTech:
Advanced roll to roll converting machines for the most complicated converting
Delta machines have “significantly improved” Tapecon’s manufacturing process, says Gebera, enabling them to, for example, convert skin biocompatibility materials, adhesives, and multilayer conductives.
“We can now handle these delicate materials with very low tension and integrate the discrete parts into the continuous web production,” Gebera says.
Confidence in the right tool for medical device manufacturing
When Tapecon has to meet exceedingly tough standards, they rely specifically on Delta ModTech machines because, in Gebera’s words, they’re “the right tool for the job.”
Cribbin adds, “Because we are ISO 13485 and 9001 registered, we typically choose Delta machines for the most highly regulated products.
“We have confidence in the machines and their ability to produce a consistent product that’s going to meet regulations.”
Ryan Cribbin, Continuous Improvement Lead, Tapecon
Responsive support from a team with a “Rolodex of ideas”
That confidence is amplified by knowing they have Delta engineers to collaborate with, especially when designing first-time products. More specifically, Delta has helped Tapecon optimize press maps, validate product concepts, and maximize the capabilities of their machines.
In fact, Cribbin says the Delta team makes themselves “very available” at any point during the production process to provide insights. “When we reach out, they can basically run through a Rolodex of ideas that help us improve our products and serve our customers.”
Throughput
With Delta ModTech’s support, Tapecon has achieved results such as the following:
Enhanced efficiency
For truly effective manufacturing, Tapecon must do more than meet demanding specs and regulations. The company needs to do those things in as streamlined a manner as possible.
“Without question, Delta ModTech has enhanced our ability to produce high quality medical devices with greater efficiency and reduced overall material waste.”
Michael Gebera, Director of Operations, Tapecon
Quicker product launches
Clients understandably have a need for speed when it comes to a new product hitting the market. And with Delta ModTech’s help, Tapecon has one more advantage to helping them get there faster.
Cribbin says Delta helps Tapecon engineers understand the application and visualize the production process. “That ultimately means we can have quicker launches to start on new products.”
Greater ability to push the bounds of what’s possible
Tapecon also has a greater ability to meet the increasingly challenging specs of customers. Cribbin cites an example of Delta helping to provide a potential solution for slitting extremely narrow webs.“We’re always trying to push the bounds with our customer base. And sometimes that means pushing the bounds of the machines, and Delta ModTech is always ready to help us do that,” he says.
OVERCOME YOUR BIGGEST CONVERTING AND PACKAGING CHALLENGES
Published on Feb 11 2025
Categories: Case Studies
Next Post
Pack Expo Southeast
Previous Post
ICE Europe 2025