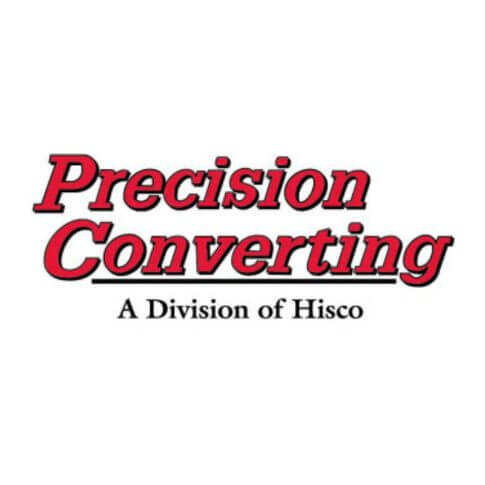
Helping Precision Converting Generate a 4x Productivity Increase
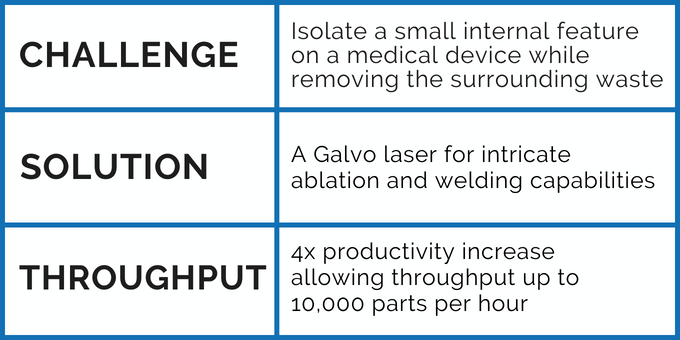
Since 1988, Precision Converting (a division of Hisco) has always met fabrication challenges head-on. Founded in 1988 in Anaheim, California, their converting team has worked with a variety of industries to customize and efficiently fabricate high quality parts for OEM designs in bonding, sealing, shielding, and thermal components.
This time, the Precision Converting team was challenged with a product for a large medical diagnostics company. Because the product could not be manufactured with conventional rotary fabrication methods, Precision Converting turned to a longtime partner Delta ModTech for a solution.
Challenge
The product was an adhesive component within a device that required assembly automation.
The size of the feature was too small for the use of conventional rotary dies, and Precision Converting was unable to isolate the small adhesive components from the surrounding areas while maintaining reliability and part compliance.
“Conventional rotary fabrication methods only achieved 50% compliance with customer specifications,” said Jeff Oldford, Engineering Sales Representative at Precision Converting.
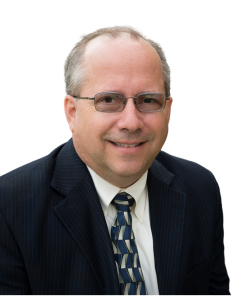
The biggest problem was removing the waste surrounding the small adhesive component. “We would either pull up the feature with the waste, or the feature would remain and the waste wouldn’t strip out of the matrix,” Oldford said. “We needed to develop a completely different cutting process.”
Precision Converting reached out to Delta ModTech with the challenge.
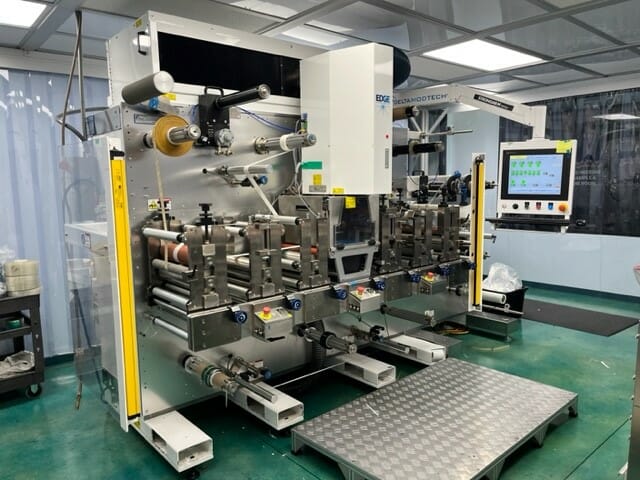
Solution
To isolate the small components and remove the waste, Delta’s engineers suggested using a Galvo laser instead of a traditional rotary die.
In the modified process, the Galvo laser was used to first cut around the feature. Because lasers physically remove material in lieu of conventional rotary dies — which only pierce the material — Precision Converting was able to isolate the feature from the surrounding adhesive waste.
“Since the galvo laser is fully programmable, we were able to make several passes around the feature and further isolate it,” added Vice President of Fabrication George Cailouette. “Part compliance increased from 50% to near 100% using galvo laser fabrication methods.”
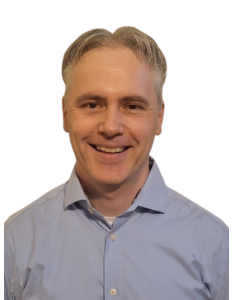
Throughput
In addition to the part compliance, the Galvo laser’s ability to weld provided much more efficient waste removal compared with prior techniques.
Precision Converting had started at a run rate of 11 feet per minute. Through learning and continued development of the process, the run rate increased to 48 feet per minute. “That’s a 4x increase in productivity,” said Engineering Sales Representative Trevor Mello.
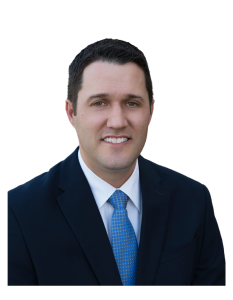
The improved productivity has also helped with meeting customer production demand.
Delta ModTech also provided ongoing training and technical support, which helped dramatically reduce the overall defect rate to 2 parts per 1000. “Our machine is connected online with Delta. Our operators will call them directly, and we get help right away,” Mello said.
The support continues whenever Precision Converting adds a new capability, such as a recently added automated vision system.
“They are a key part of our growth”
The new Delta capability resulted in a successful project, but it has also allowed Precision Converting to pursue new opportunities with other companies, and continuously expand their bottom line.
They’ve experienced a growth rate of 26% compounded annually over the last eight years within their division of Hisco. It’s why George Cailoutte said: “We view Delta as a strategic business partner, not just an equipment provider. They’re a key part of our growth.”
And whenever one of those new opportunities arises, Delta is there to help solve their toughest challenges. Added Trevor Mello: “I don’t think we’ve brought something to them yet where they said they couldn’t help us.”
OVERCOME YOUR BIGGEST CONVERTING AND PACKAGING CHALLENGES
Published on Sep 13 2023
Last Updated on Aug 07 2024
Categories: Case Studies, Converting, Die Cutting, Lasers
Previous Post
Label Expo Europe